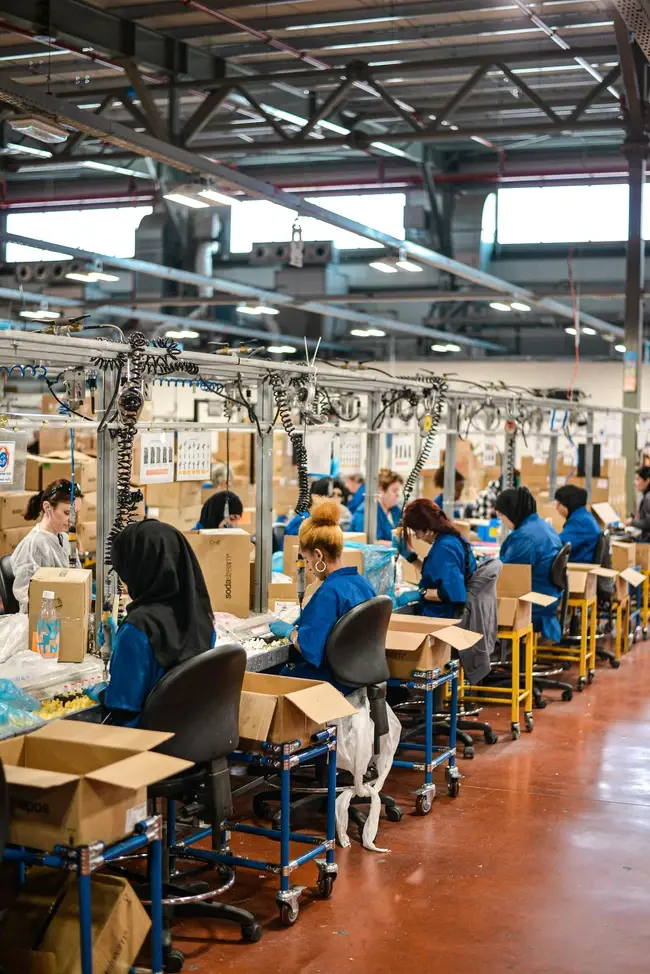
If the shortage of skilled workers is keeping you up at night, you’re not alone. While building and maintaining a skilled workforce has long been a challenge for the UK’s manufacturing sector, the issue has only been intensified by digitalisation and Brexit; and more recently, by issues such as wage inflation.
In fact, Make UK’s latest research found that more than a third (36%) of manufacturing vacancies are proving hard to fill. Compared to an average rate of 24% across other industries, it’s clear that attracting and retaining a quality workforce remains a significant challenge for British manufacturers. So, what processes and technologies will attract and retain the workers needed for success in any economic environment?
Moving towards human centricity
In the “old days” it was enough to pay just a little more to attract and retain workers, but that’s no longer the case. Today’s employees – including “deskless workers” – expect and deserve more. They not only want decent pay, that want to be heard and valued throughwith input in decision-making, opportunities for training and career growth, as well as a sense of purpose. They also want more flexibility and control over when they work, just like their corporate counterparts.
Despite this, almost 60% of companies have little to no flexible technology solutions in place to support deskless shift workers, and the manufacturing sector is certainly no exception. Yet, the business case for these solutions is clear, with Gartner highlighting that employers who use human-centric work models and technologies – in which “employees are treated as people, not just resources” – are three times more likely to experience high intent to stay and minimised levels of fatigue.
Modern, human-centric workplace technologies will therefore play a critical role in helping manufacturing companies to better meet the needs of workers, be more agile and responsive in the face of variable demand and make traditional human resource processes more efficient. Only then will managers be able to spend more time on strategic tasks, like improving warehouse and distribution centre operations, which is necessary for the on-time flow of goods.
Specifically, modern workforce technologies will enable manufacturing companies to transition towards human-centric employee experience (EX) models by:
- Offering scheduling flexibility – Implementing technology that gives staff a larger voice in when and how much they work will be a major step toward a more engaging workplace experience. Workforce technology builds scheduling flexibility while allowing managers to ensure optimal coverage, monitor for fatigue, and comply with union agreements, company policies, and regulations.
- Engaging in real-time communications – With a strong tech platform rooted in a consumer-grade experience, employees and managers can connect through real-time communications that are integrated into the flow of work. This capability increases scheduling agility, reduces overtime, mitigates burnout, and makes accessing information easier. In addition, real-time feedback loops give workers a chance to be heard and contribute to the organisation’s success.
- Streamlining work processes – Modern workforce systems enable easy access to resources like company announcements, work guides and development materials. Most importantly, they deliver the training and information that employees need as they are working, which saves them from having to search for information, guess the correct way of performing a task, stay after their shifts to sort through updates, or attend training on days off.
- Supporting career development – Newer generations of employees are eager to learn new skills but tend to do so differently than prior generations of workers. For example, younger workers tend to prefer “micro training” in the form of video snippets to hours of classroom training. Modern workforce management technologies can offer dynamic content, send reminders about certifications, or even automate training reminders based on the work employees are scheduled to do. These solutions also allow businesses to easily identify workers who are suited for cross-training opportunities, support on-the-job learning by pairing new joiners with veteran workers, and build a multi-skilled workforce where employees can step in quickly as things change.
- Optimising labour – Many manufacturing companies still use manual methods to fill gaps in scheduling shifts. Yet, these outdated approaches create challenges in planning and managing large groups of employees, often at a significant cost to your organisation. Fortunately, using workforce technology, companies can automate and optimise staffing levels based on criteria like lowest cost, even when regulatory or union rules govern decisions. Workforce technologies allow businesses to match labour supply with the actual labour needed to meet current demand. Ultimately, this helps them avoid costly and unnecessary overtime when actual work does not align with planned work and staff assigned.
- Modernising the EX-tech stack – Engaged employees take fewer days of unplanned leave and are more likely to feel a sense of loyalty. While the long-term goal is to implement capabilities that make your organisation an employer of choice, that doesn’t happen overnight. However, modern workforce technologies allow you to change processes incrementally. For example, you could start by digitising scheduling, add annual leave management and labour optimisation capabilities later, and finally, incorporate features like employee feedback loops and scheduling flexibility.
With the shortage of skilled workers in Britain’s manufacturing sector costing the UK £7 billion in lost economic output, now is the time to invest in modern workplace technologies that enable human-centric EX strategies. The companies that deploy this human-centric approach will remain competitive and grow even in the most volatile of market conditions.
Comments ( 0 )